MAE Senior Designs
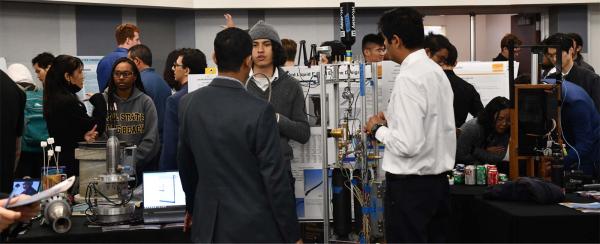
Mechanical and Aerospace Engineering students design, develop, fabricate and fund engineering projects entirely at CSULB during their one-year senior design class. This experience is at the core of the College of Engineering’s emphasis on project-based learning. The teams start with customer needs, then begin working on conceptual design proposals. At the end of the year, a demonstrable article is presented at the Senior Design Expo.
Roughly 45 student projects were defined and developed in 2022 and 2023, focusing on the following categories:
- Green Energy (Ocean and Wave Energy)
- Liquid and Solid Rockets
- Additive Manufacturing
- Composite Structures and Coating for Aerospace
- Automation for Fastening and Assessment
- Miscellaneous Topics
Thanks to the many SoCal companies that mentored our students, including Boeing, Northrop Grumman, NextGen Aeronautics Corp. Air Force Research Laboratory, Techtronics and more.
Design and development of liquid rocket static fire test stand
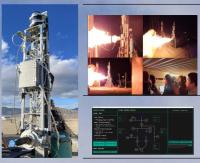
The team developed and successfully tested a pressure fed propulsion static fire test stand for a Nitrous/Kerosene heatsink engine built at CSULB. The stand can pressurize to a maximum of 500 psi in the propellant tanks and to 2000 psi in the COPV. The main ball valves are actuated by a pneumatic powered linkage system uniquely designed and manufactured in house. For added safety, Nitrous can be filled remotely and the GUI gives pressure readings in the high-pressure region for nitrogen, the two propellant tanks and in the engine.
Scaled 1:100 offshore Wind Turbine prototype
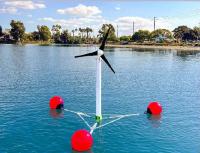
This project was the culmination of collaborating to design and fabricate an offshore wind turbine platform. This project was envisioned to provide proof of concept for a prototype prioritizing DFM, alternative materials used in manufacturing, and the stability of the platform. The platform was able to successfully float while carrying a 25-pound turbine, mounted at over six feet. The modular design allows the platform to be taken apart easily and modified in case any components need to be upsized for the next iteration.
Turbojet engine characterization
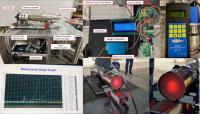
The purpose of this project was to determine whether a catalytic converter could be designed to reduce emissions without compromising engine thrust. The team engaged in designing, building, and testing a functional catalytic converter for a turboshaft. A modified SW120B turbojet engine was used to characterize the engine performance. Thermocouples for thermal loading, a load cell, and an emissions tester were incorporated to assess the performance.
Full-scale 1:1 UAV
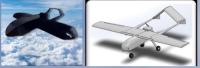
A full scale UAV was designed, analyzed in ANSYS and manufactured by FDM and Carbon Fiber Polymer (CFRP) composite. A fly ready commercial UAV was modified and used as a basis for the geometry. The main idea was to develop a low-cost UAV with short lead-time. A collapsible wing concept prototype was also developed to be merged as an alternative to the fixed wing production.
Supportless and Conformal Fused Deposition Modeling Three-Dimensional Printing via 5-Axis
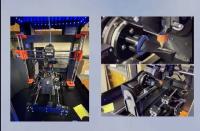
Introducing the advanced 5-axis 3D printer—an upgrade from the traditional 3-axis models. This innovation allows for more intricate and precise designs. This project focuses on comparing prints from both 5-axis and standard 3-axis printers, showcasing the different layer orientation capabilities of the former while also being supportless. This multi-axis movement not only unlocks new design possibilities but also enhances overall manufacturing potential. Modifying an already existing three-axis 3D printer, the Prusa i3 MK3S model, with guidance and inspiration from the open-source project Open5x, this project enabled the team to develop and test a 5-axis FMD.
Cooling vest using thermal plate and cold gas
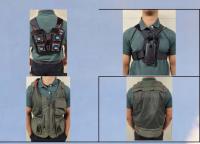
The objective of this project is to elevate occupational well-being for field workers in hot conditions, and reduce the risks of heat related illness. The first design utilizes four thermoelectric cooling plates powered by a 5 volt battery pack. The modular design allows for adaptability to a wide range of sizes, additionally allowing for the plates to be connected to pre-existing safety equipment. The second design utilizes CO2 as a cooling gas, with a variable flow regulator to adjust to the user's cooling needs. These two designs provide a mobile cooling solution to suit the needs of the user.
CFRP reinforcement for utility poles
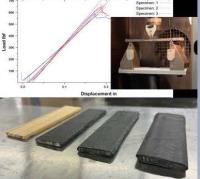
Utility poles are an essential part of modern society as they carry the lines that deliver power and information across the country. Over time, the structural integrity of these wooden poles degrades, and they must be replaced. This can be costly and leave many without power for a time. Besides this, there is the environmental issue of cutting down more trees for use as poles. This project sought to test how a carbon fiber wrap reinforcement may provide a solution to these problems by extending the service life of a pole. Wood samples were wrapped in carbon fiber and put through a three-point bending test to determine the improvements in durability.
CFRP patch for metallic structures
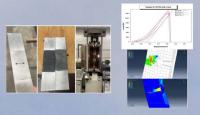
In the defense industry, damaged metallic parts caused significant time and money to be spent on disassembling structures and replacing components. To reduce these expenses, many companies sought a more cost-effective solution. This project aims to establish an efficient procedure for repairing such parts, specifically creating a composite patch repair for aircraft-grade Aluminum. This involves studying various experiments, analyzing material properties, and conducting multiple fatigue tests to gauge the effectiveness of the repair.
Low-cost COPV for hydrogen fuel and liquid rocket tanks
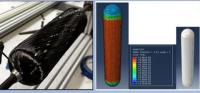
Our project concentrated on enhancing the COPVs' structural integrity without adding weight, a critical factor for space launch efficiency. The project's cornerstone lies in its optimized fiber winding angles, using the most modern research data results to optimize strength when it comes to applied stresses, particularly shear and tensile forces when the tank is under pressurization. This optimization ensures our COPVs offer increased strength-to-weight ratios, making them exceptionally suitable for demands of high performance-low weight.
Multi-fuel turbojet engine
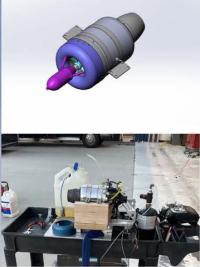
The multi-fuel turbojet engine project studies the performance of the Jetcat P120 engine when run on kerosene and liquid propane. Modern recreational jet engines run strictly on liquid fuels, such as Jet-A, kerosene, and diesel, but have potential to run alternative cleaner burning fuels. Propane is a reasonable alternative for use in unmanned aerial vehicles as it can be easily acquired, is cheaper, burns cleaner, and has a higher energy content when compared to kerosene and diesel. The team successfully ran tests for kerosene and propane and extracted thrust, temperature, and rpm data from the monitoring systems.
Introduction and Refinement of Yttria Nanoparticles into 316L Stainless Steel for Metal Additive Manufacturing
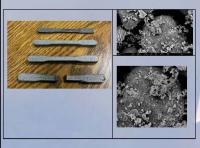
This project focuses on exploring the introduction of Yttrium-Oxide nano-particles into 316L Stainless Steel metal powder, in order to establish new boundaries in relation to thermal and mechanical properties in metal additive manufacturing using SLM process. The outcome is the optimal refinement in the creation of an 316L Stainless Steel and Yttria-Oxide metallic powder by varying the percentages of Yttria-Oxide, and by adjusting the time intervals and revolutions per minute used during Planetary Ball Milling.
Mechanical Rocket Recovery System
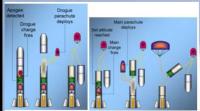
The main purpose of this project was to build a successful rocket recovery system that a single person could assemble which doesn’t require any special license for pyrotechnics that could be armed and disarmed externally to the rocket for safety. Our design used a dual-deployment mechanical rocket recovery system consisting of a drogue parachute deployed at apogee and a main parachute at a different desired altitude.
Liquid rocket for R&D
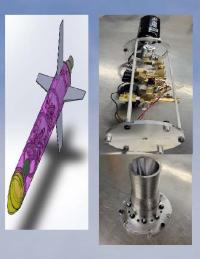
The objective of this project was to design modular liquid rocket sub-systems (propulsion, engine, recovery, avionics and structure) for college and universities. Most rocketry kits are limited to solid propellant systems. Our aim was to build a liquid propellant system with readily available propellants and an altitude goal of 10,000 ft. A simple modular design allows for future modification and research. Sub-systems including avionics, propulsion, recovery, and aero are modifiable for further research. Our propellant choice was diesel and N2O. The rocket has a blowdown propulsion system with an impinging injector and heatsink engine.
Design and Development of Additively Manufactured Liquid Rocket Engine
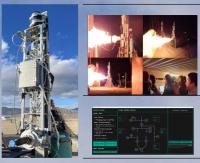
This project is an RP-1/LOX liquid rocket engine design that takes advantage of the metal 3D printing technology’s ability to produce complex geometry to optimize cooling efficiency. Thermal control is essential for the feasibility and longevity of a rocket engine. This design features 58 cooling channels with variable crosssections for effective heat dissipation at high-heat regions while also preventing the thermal decomposition of RP-1. To characterize the design of the engine chamber contour and other components, a heat-sink type test engine is CNCed along with the injector plate and the LOX plate. At the maximum design chamber pressure of 350 psi, the engine’s estimated delivered performance at sea level is 777 lb-f with a specific impulse of 251 seconds.
Exoskeleton for Parachute Landing Fall
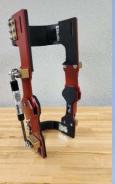
The problem the group is attempting to improve is that which are common to paratroopers—injury. Parachute landing fall (PLF) is the current method paratroopers and parachutists use when landing on the earth. The method calls for a person to roll when landing to disperse the impact force across one’s entire body. The PLF method, however, causes knee, back, ankle, and hip injury over time. To improve this problem, the lower limb exoskeleton was created to reduce overall chance of injury by increasing the time of impact. This is achieved by supporting the hamstring and calf muscles with an aluminum frame and gas springs.
Universal Drone Base Plate Attachment
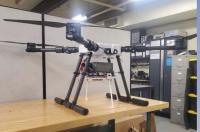
The objective of this project was to design an attachment for larger drones capable of multiple functions. The components on the attachment include a rangefinder to measure the altitude the drone is flying at, an infrared camera to detect damage on infrastructure, a claw mechanism capable of picking up and placing packages, and a transceiver to send and receive data wirelessly. Steel wire attached to a linear actuator allows the claws to open and close on command. An Arduino Uno mounted on the drone attachment was programmed to collect the data and send it to the user through a secondary Arduino.
Thread Fastening Robotic Arm with Machine Vision
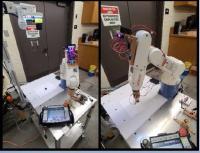
The purpose of this project was to explore automation in the manufacturing industry, by demonstrating a robotic arm utilizing machine vision to locate and thread a bolt, simulating what could be expected on an assembly line. The system can be broken down into three main parts: DENSO Robotic Arm, COGNEX Camera, and a 3-D Printed Arduino controlled End-Effector which utilizes a limit switch and electromagnet to both detect and grip a bolt.
Composite Patch for Metallic Structures
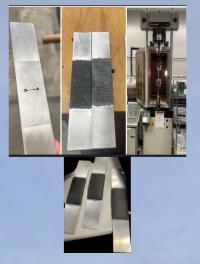
Within aerospace industries, damaged parts led to excessive time and money being spent for structure disassembly and part replacement. To limit these expenditures, many companies began exploring a more cost-effective way to solve this problem. The goal of this project is to establish an effective and repeatable procedure for this type of repair. More specifically, to create a composite patch repair of aircraft grade Aluminum by studying multiple different experiments, analyzing the material properties of each product to be assembled, and performing multiple tests on the effectiveness of the repair. The fatigue properties were improved by 50%.
Plastic recycling for 3D printing filaments
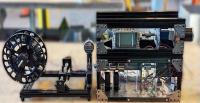
The goal of this design project was to create an all-inone machine that can recycle certain plastics to be reused as 3D filament. The machine will be able to take raw plastic, waste plastics, and plastic filament from previously failed prints. The machine will be composed of a grinder, extruder, cooler, and winder all together within the design of the machine. Several machines on the market currently have these components as separate machines that function together in a line, but for this to be as consumer-friendly as possible this project has brought together all functioning components into a compact version.
Coatings for aerospace and wind-turbine structures (thermal barrier coatings and erosion coatings)
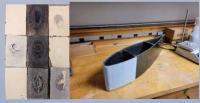
A study on the effects of heat on different applications of Yttrium based thermal barrier coatings. Many of the tests consists of different application methods, using them on both sheet aluminum and inconel type metal sheets. The end results show that yttrium coatings are reliable when coated appropriately. Leading-edge erosion is a primary concern for the offshore and desert wind industry. Wind turbine erosion coating presents the results of an investigation into the addition of nanoparticles as internal structures within the coating, which can scatter the stress waves from impact.
Composite Overwrapped Pressure Vessel
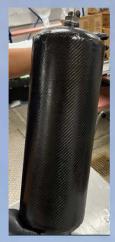
COPV tanks are utilized within the aerospace industry as a light-weight, more effective alternative to metal pressurization tanks. The COPV tank is vital to success in launch and flight operations, due to their abilities to expand and hold the needed pressure for optimal propellant performance. The implementation of the composite allows for a greater allowable stress, leading to a greater efficiency and mission success. This specific design is made to hold hydrogen at a pressure of 3-5k psi. This was done through the use of pre-preg and raw carbon fiber that was wrapped through the use of automated manufacturing.
Archimedes’ Principle Overflow Tank (APOT)
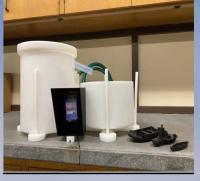
The Archimedes’ Principle Overflow Tank (APOT) is a tabletop buoyancy measurement device designed for use in quality control processes. A test specimen is placed into the overflow tank and weighed dry in order to get the object’s mass, which progresses through the device’s computing system. The part is then taken out and placed into the main tank with the working fluid present. Displaced water then flows into the overflow tank where it is weighed via a button-style load cell and transmitted once again through the sensor, running data through an Arduino board and displaying the item’s mass, volume, and density on the touchscreen. This overflow application of Archimedes’ Principle allows for the accurate measurement of more complex manufactured parts in industry.
Electromagnetic Auxiliary Automotive Brake
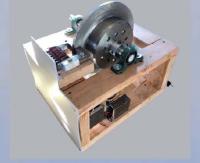
The intent of this project was to create an electromagnetic eddy current braking system for automobiles. The c-clamp shaped magnet is wrapped by 16-gauge copper wire and powered by two 24V batteries to stop the rotor disks on the vehicle. The magnetic brake was designed, manufactured, and tested for reliability and effectiveness as an additional braking system on a car. A testing bench was created to emulate the braking process of a car in a visible scale.
Water Pipe Power Generator
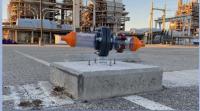
The water pipe power generator produces energy from the water flowing through the pipes. Our turbine is held by two stoppers and placed horizontally to minimize the potential sealing issues compared to if it had been positioned vertically. Magnets are placed around the turbine and copper magnet coils circle the outside of the pipe. This device can be placed for in-home use.
Offshore Floating Wind Turbine Spar Buoy Platform
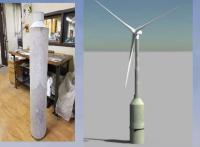
Two groups collaborated together to create a prototype of an offshore wind turbine generator that floats on a buoy and is tethered to the seaboard. Group 3-2 took charge of the “buoy structure” whereas Group 5-2 handled the “concrete tower and turbine structures”. The purpose of this project was to design a floating platform for an offshore horizontal wind turbine. The concept utilized was a spar buoy design that consisted of a large air cavity, environmentally friendly geopolymer concrete, and a steel ballast. The goal was to build a scaled down model large enough to keep a 50lb turbine and tower afloat all while maintaining stability through the buoy's low center of gravity.
3D printed brushless DC motor
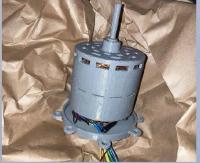
As the use of electrical motors is increasingly more abundant in most industries today, likewise, the need for finding alternative methods or motor materials to produce quality motors increases. This project explores the implementation of alternative materials, mainly 3D printed plastics, to construct a fully functional Brushless DC (BLDC) motor. Through the use of plastics and plastic-composites with additive manufacturing, the potential to develop cheap yet efficient motors is demonstrated.
CNT hair flow sensor
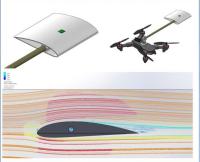
Mother nature has allowed many organisms to develop extra sensory systems to cope with ever-changing environmental situations. These sensory organs are very energy efficient, extremely sensitive, and facilitate near-instantaneous reactions to stimuli. Artificial implementation of these structures, to create “fly-by-feel” systems, could pose a phase shift in the way aircraft and aerodynamic structures are designed and controlled. A system such as this could take measurements directly from a particular surface of an aircraft and could allow for the detection of anything from wind speed and direction, the separation of flow from a surface, or even the transition from laminar to turbulent flow. Our group has recreated the growth process, assembly, and implementation of carbon nanotube-based artificial hair sensors to extract useful data.
Cuttlefish underwater robot
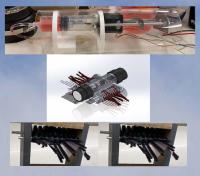
The purpose of creating a cuttlefish-like robot is to educate and spark the interest of the next generation of students that could be interested in becoming Engineers, specifically for this project with an emphasis on Biomechanics. The significance of the cuttlefish project is taking a proven design and creating a cheaper, lighter, and less complicated version for education purposes. NextGen aeronautics has already built a large full scale cuttlefish robot at their facility and there is a need for a smaller scale one that can swim as fast as possible, have a power system that lasts as long as possible, and is small/light enough to fit in your hands. In order to produce the best suited prototype, there is a lot of consideration to be taken in ranging from the material of the body/ribs/fin, communication, power supply, motor, depth control, and weight of the system.
Contact
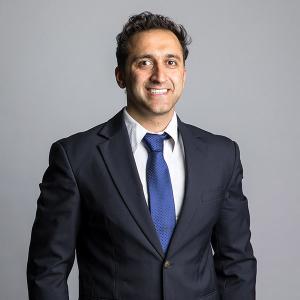
Mahdi Yoozbashizadeh
Associate Professor
Office: ECS-624
Phone: 562.985.5257
Email: mahdi.yoozbashizadeh@csulb.edu
Office Hours: Mon. 11:45-1:00 p.m.